Im Rahmen der zweimal jährlich in Ludwigshafen stattfindenden Großschadensalarmübung trainierten im September 2023 rund 100 Einsatzkräfte der Gefahrenabwehr für den Ernstfall. Das Szenario: Aufgrund einer defekten Dichtung kommt es an einer Anlage zum Austritt einer lösemittelhaltigen Flüssigkeit mit nachfolgender Entzündung und Verpuffung. Übungen dieser Art sind fester Bestandteil des präventiven Sicherheitskonzepts unserer Standorte.
Anlagensicherheit ist Kernelement einer sicheren, zuverlässigen und somit zukunftsfähigen Produktion. Mit unseren umfassenden Sicherheitskonzepten wollen wir Mitarbeitende, Kontraktoren und die Menschen in der Nachbarschaft unserer Standorte bestmöglich schützen sowie Sach- und Umweltschäden vermeiden.
Strategie und Governance
Im Bereich der Anlagensicherheit setzen wir auf umfassende Präventivmaßnahmen und verbessern kontinuierlich unsere Produktionsprozesse. Chancen ergeben sich insbesondere im Bereich der Automatisierung und Digitalisierung von Prozessen. In unseren komplexen Produktionsanlagen kann es nichtsdestotrotz zu Ereignissen kommen, die potenzielle Auswirkungen auf Mensch und Umwelt haben. Chancen und Risiken aus dem Bereich der Anlagensicherheit erfassen wir systematisch im Rahmen unseres allgemeinen Chancen- und Risikomanagements.
Ziel 2030 a
≤ 0,10
Reduzierung der weltweiten Anlagenereignisse mit hohem Schweregrad je 200.000 geleistete Arbeitsstunden b
a Im Jahr 2023 haben wir die Zielgrößen im Bereich Sicherheit angepasst.
b Dies umfasst die Arbeitsstunden von BASF-Mitarbeitenden, Leasingkräften und Kontraktoren.
Gefahrenabwehr bedeutet für uns, zu jeder Zeit und an jedem Ort auf ein mögliches Ereignis vorbereitet zu sein.
Unsere Produktionsanlagen sind der Kern unseres Geschäfts. Um eine zuverlässige und sichere Produktion zu gewährleisten und Ereignissen in unseren Anlagen entgegenzuwirken, geben wir weltweit verbindliche Standards zur Anlagensicherheit vor. Umsetzung und Einhaltung der gruppenweiten Richtlinien und lokalen Vorgaben liegen in der Verantwortung unserer Standorte und Gruppengesellschaften. Die Corporate-Center-Einheit „Environmental Protection, Health, Safety and Quality“ (EHSQ) überprüft im Zuge von Audits regelmäßig, ob die Vorgaben eingehalten werden.
Wir verfolgen anspruchsvolle Ziele zur Anlagensicherheit. Unsere Fortschritte in der Zielerreichung überprüfen wir regelmäßig als Teil des kontinuierlichen Verbesserungsprozesses. Unsere Ziele und Leistungsindikatoren für die Arbeits- und Anlagensicherheit haben wir im Jahr 2022 einer kritischen Prüfung unterzogen. Seit 2023 fokussieren wir uns auf Ereignisse mit hohem Schweregrad. Basis der Berichterstattung bilden weiterhin die etablierten Industriestandards, wobei wir den Menschen stärker in den Mittelpunkt rücken.
Globale Ziele und Maßnahmen
Bei Planung, Bau und Betrieb unserer Anlagen legen wir weltweit anspruchsvolle Sicherheitsmaßstäbe an. Diese erfüllen die lokalen gesetzlichen Anforderungen und gehen zum Teil darüber hinaus. Unsere weltweit gültigen Richtlinien geben den Rahmen für den sicheren Bau und Betrieb unserer Anlagen sowie den Schutz von Mensch und Umwelt vor. Unsere Fachleute entwickeln für jede Anlage ein Schutzkonzept, das von der Anlagenkonzeption bis zum Ende der Produktion die wesentlichsten Aspekte von Sicherheit, Gesundheits- und Umweltschutz berücksichtigt und entsprechende Schutzmaßnahmen festlegt.
Um weltweit das hohe Sicherheitsniveau unserer Anlagen über den gesamten Lebenszyklus zu erhalten, überprüfen wir im Rahmen von „Implementation Checks“ in regelmäßigen Abständen und abhängig vom Risikopotenzial in allen Betrieben die Implementierung unserer Schutzkonzepte. Dies gilt auch für die termingerechte Umsetzung der vorgeschriebenen Sicherheitsbetrachtungen und der daraus resultierenden sicherheitstechnischen Maßnahmen. Die Sicherheits- und Schutzkonzepte unserer Anlagen aktualisieren wir regelmäßig. Hierbei berücksichtigen wir insbesondere neue Erkenntnisse, technologische Möglichkeiten und regulatorische Entwicklungen.
Als Berichtsgröße nutzen wir die Anzahl der Anlagenereignisse mit hohem Schweregrad (High Severity Process Safety Incidents, hsPSI) je 200.000 geleistete Arbeitsstunden. Wir haben uns das Ziel gesetzt, bis 2030 eine Rate von höchstens 0,10 Anlagenereignissen mit hohem Schweregrad je 200.000 geleistete Arbeitsstunden zu erreichen. 2 Im Jahr 2023 verzeichneten wir weltweit eine Rate von 0,05 hsPSI je 200.000 geleistete Arbeitsstunden. Die Rate der gesamten Anlagenereignisse in der BASF-Gruppe lag bei 0,3 im Jahr 2023 (2022: 0,3). Wir untersuchen jedes Ereignis detailliert, analysieren Ursachen und nutzen die Ergebnisse, um geeignete Maßnahmen abzuleiten. Die Erkenntnisse teilen wir in unserem globalen Netzwerk, um uns stetig zu verbessern.
Zur Verringerung von Anlagenereignissen setzen wir insbesondere auf technische Maßnahmen, digitale Lösungen sowie auf eine Führungskultur, die Anlagensicherheit und den offenen Umgang mit Fehlern noch stärker in den Fokus rückt. Zur Stärkung des Risikobewusstseins und der Sicherheitskultur entwickeln wir unsere Schulungsmethoden und -angebote kontinuierlich weiter. So wurde beispielsweise 2023 an unserem chinesischen Standort Pudong in einem Programm zur Reduzierung von Anlagenereignissen das Thema Dichtigkeit und die Vermeidung von Leckagen in den Vordergrund gestellt und in Schulungen behandelt.
Wir fokussieren uns bei unseren Zielen auf Ereignisse mit hohem Schweregrad, um den Menschen stärker in den Mittelpunkt zu rücken.
In internen und externen Netzwerken, über unser Engagement in Verbänden wie dem International Council of Chemical Associations (ICCA), dem European Process Safety Centre (EPSC) oder dem Center for Chemical Process Safety (CCPS) sowie durch den Austausch mit Behörden bringen wir uns weltweit aktiv in die Weiterentwicklung der Anlagensicherheit ein.
2 Dies umfasst die Arbeitsstunden von BASF-Mitarbeitenden, Leasingkräften und Kontraktoren.
Fallbeispiel
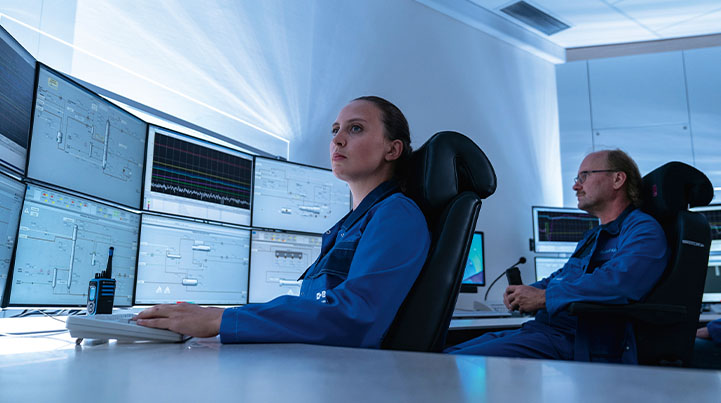
Lernen durch Simulation
Mit einem Operator Training Simulator (OTS), einem Simulator zur Schulung von Anlagenfahrern, lässt sich realitätsnah üben, was in der Praxis anzuwenden ist. Ähnlich einem Flugsimulator können anhand von OTS-Systemen Prozesse komplexer chemischer Anlagen simuliert werden.
Neue Mitarbeitende können sich auf diese Weise praxisnah in ihr Arbeitsfeld einarbeiten. Sie trainieren, wie sich die Anlage steuern lässt, welche Ventile unter welchen Bedingungen geöffnet oder geschlossen werden müssen und welche Trendkurven im Prozessleitsystem besonders im Blick zu behalten sind. Darüber hinaus können mit einem OTS Bedingungen simuliert werden, die im Arbeitsalltag eher selten vorkommen – etwa spezifische Störungen. Deswegen eignet sich der Simulator auch für Schulungen von erfahrenen Mitarbeitenden.
Durch den Einsatz von OTS wollen wir die Betriebssicherheit unserer Anlagen weiter erhöhen sowie Störungen schneller und besser beheben. Gleich mehrere unserer Unternehmensbereiche nutzen Simulatoren. So entwickelt der Bereich Petrochemicals derzeit in enger Zusammenarbeit mit der Einheit „Global Engineering Services“ OTS für alle seine Anlagencluster an dem im Bau befindlichen Verbundstandort in Zhanjiang/China. Der Vorteil, wenn bei Neuprojekten OTS zeitgleich zur Planung mitgedacht werden: Schwachstellen können bereits vor dem Bau identifiziert und behoben werden.
In Nanjing/China, Port Arthur/Texas, Ludwigshafen und Antwerpen/Belgien sind die Simulatoren schon seit einigen Jahren bei ausgewählten Anlagen erfolgreich im Einsatz.