Story
Innovative Verfahren für eine klimafreundliche Chemie
Basischemikalien sind elementare Bestandteile vieler Produkte, die Klimaschutz für unsere Kunden ermöglichen und den Menschen den Alltag erleichtern. Das Problem: Konventionelle Produktionsverfahren für Basischemikalien verursachen häufig hohe CO2-Emissionen – und haben daher mit Blick auf die ambitionierten Klimaschutzziele von BASF langfristig keine Perspektive. Im Rahmen des Carbon-Management-Programms entwickelt BASF daher innovative Technologien zur klimafreundlichen Produktion von Wasserstoff, Olefinen, Aromaten und Co.
Außen Backstein, innen High-Tech. Ein komplexes Geflecht aus Rohren, Ventilen und Messarmaturen. Im Hintergrund ein leichtes Surren, das kaum erahnen lässt, dass hier gerade Bahnbrechendes passiert.
Mittendrin Dieter Flick. „Als wir vor rund zehn Jahren mit unseren Forschungsarbeiten begannen, war keinesfalls absehbar, dass all das hier einmal Realität wird.“ Flick leitet bei BASF die Methanpyrolyse – neben der Wasserelektrolyse eines von zwei BASF-Projekten zur CO2-armen Herstellung von Wasserstoff.
Die Bedeutung von Wasserstoff für BASF-Wertschöpfungsketten
Wasserstoff spielt in der chemischen Industrie eine gewichtige Rolle. Das kleinste und leichteste Element im Baukasten der Natur ist zentraler und unersetzlicher Rohstoff für wichtige Basischemikalien wie Ammoniak und Methanol und darüber hinaus Bestandteil vieler Polymere wie etwa von Kunststoffen. Der weltweite Wasserstoff-Bedarf von BASF liegt derzeit bei rund 1 Million Tonnen pro Jahr. Davon werden allein am Standort Ludwigshafen circa 250.000 Tonnen produziert oder fallen als Nebenprodukte in der Produktion an.
Wie fast jeden Tag ist der Verfahrensingenieur auf Tour durch die Testanlage, die seit 2021 am Standort Ludwigshafen läuft. Gerade prüft er mit seinem Kollegen Florian Schachtschabel wichtige Anlagenparameter wie Druck und Temperatur. „Die Idee zur Methanpyrolyse gibt es schon seit den 1960er Jahren. Bislang scheiterte sie allerdings immer an der technischen Umsetzung“, so Flick.
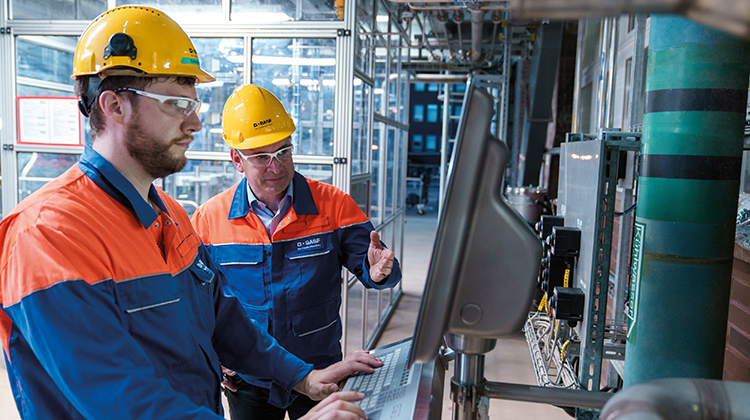
Dabei ist das Prinzip der Methanpyrolyse denkbar einfach: Methan (CH4), der Hauptbestandteil von Erd- oder Biogas, wird bei hohen Temperaturen direkt in seine Bestandteile Kohlenstoff (C) und Wasserstoff (H2) aufgespalten. Im Vergleich zum gängigen konventionellen Verfahren zur Wasserstoffgewinnung auf Basis fossiler Energieträger, der sogenannten Dampfreformierung, entstehen dabei kaum CO2-Emissionen.
Wie so oft bei innovativen Technologien, steckt die Tücke jedoch im Detail. „Von der Idee bis zur Realisierung ist es bei einem solchen Projekt ein sehr weiter Weg. Wir mussten nicht nur den Pyrolyseprozess im Detail erforschen, sondern beispielsweise auch verschiedene hochtemperaturfeste Werkstoffe testen und ein neues Beheizungskonzept entwickeln. Das geht nur mit Teamgeist, Ausdauer, Expertise aus den unterschiedlichsten Bereichen und jeder Menge Herzblut“, so Flick. Das Bundesministerium für Bildung und Forschung fördert das Projekt.
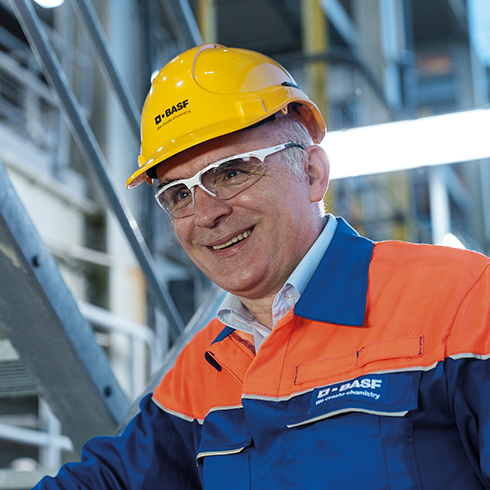
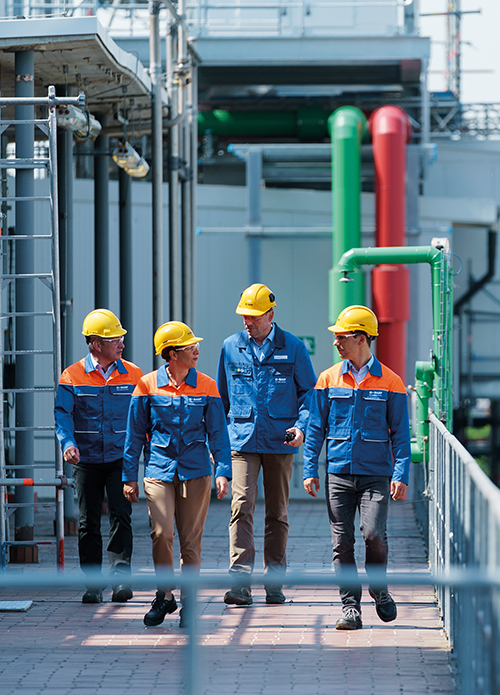
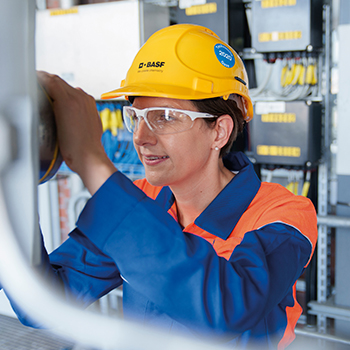
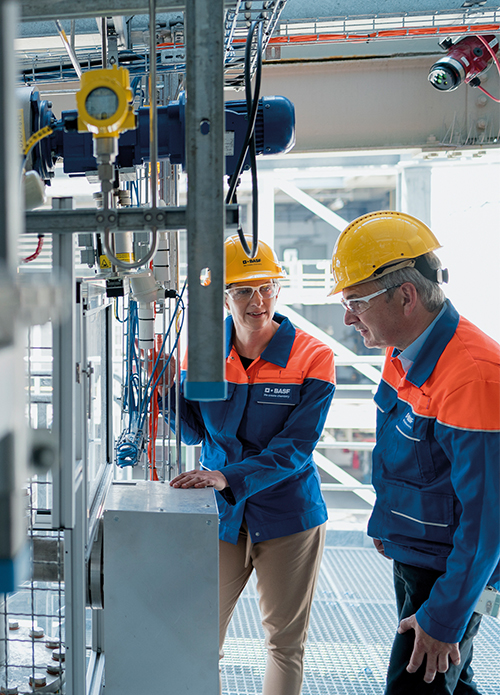
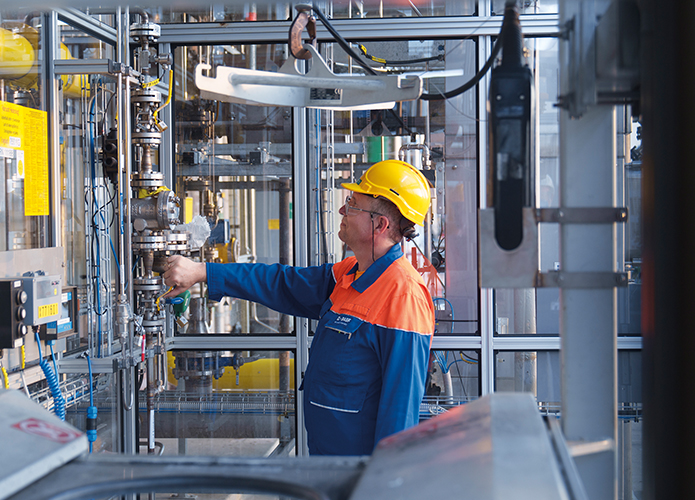
Die Besonderheit der Testanlage, die sich über mehrere Stockwerke erstreckt, ist das innovative Reaktorkonzept mit dem weltweit ersten, industriell eingesetzten Kohlenstoff-Wanderbett. Es ermöglicht einen hohen Wirkungsgrad und eine hohe Prozesseffizienz (weitere Erläuterungen im Film). „Wenn sich das Verfahren in der Testanlage bewährt, folgen im nächsten Schritt die Skalierung und der Bau einer Pilotanlage“, blickt Flick in die Zukunft.
Der Prozess der Methanpyrolyse
Neben Wasserstoff entsteht bei der Methanpyrolyse fester, reiner Kohlenstoff – ein wertvoller Rohstoff, der in der Natur so nicht vorkommt. Wenn die Testanlage stabil läuft und ausreichende Mengen des Kohlenstoffs zur Verfügung stehen, will das Team in einer zweiten Phase des Projekts prüfen, welche Anwendungen für den entstehenden Pyrolyse-Kohlenstoff technisch realisierbar und wirtschaftlich sind.
Spätestens im Jahr 2030 soll die Methanpyrolyse im großtechnischen Maßstab verfügbar sein. Eine wichtige Zielmarke, denn bis dahin will BASF die Treibhausgasemissionen im Vergleich zu 2018 um 25 % senken. Bis 2050 strebt BASF Netto-Null-Emissionen hinsichtlich der Treibhausgase der Produktionsstandorte und des Energieeinkaufs an. „Neue CO2-freie und CO2-arme Technologien und Produktionsverfahren sind auf diesem Weg ein wichtiger Hebel“, sagt Dr. Lukas Mayr. Der Chemiker leitet bei BASF das Carbon-Management-Forschungs- und Entwicklungsprogramm, in dem zahlreiche Projekte zur klimafreundlichen Produktion von Basischemikalien mit Hochdruck vorangetrieben werden. Wichtig dabei: Technologieoffenheit.
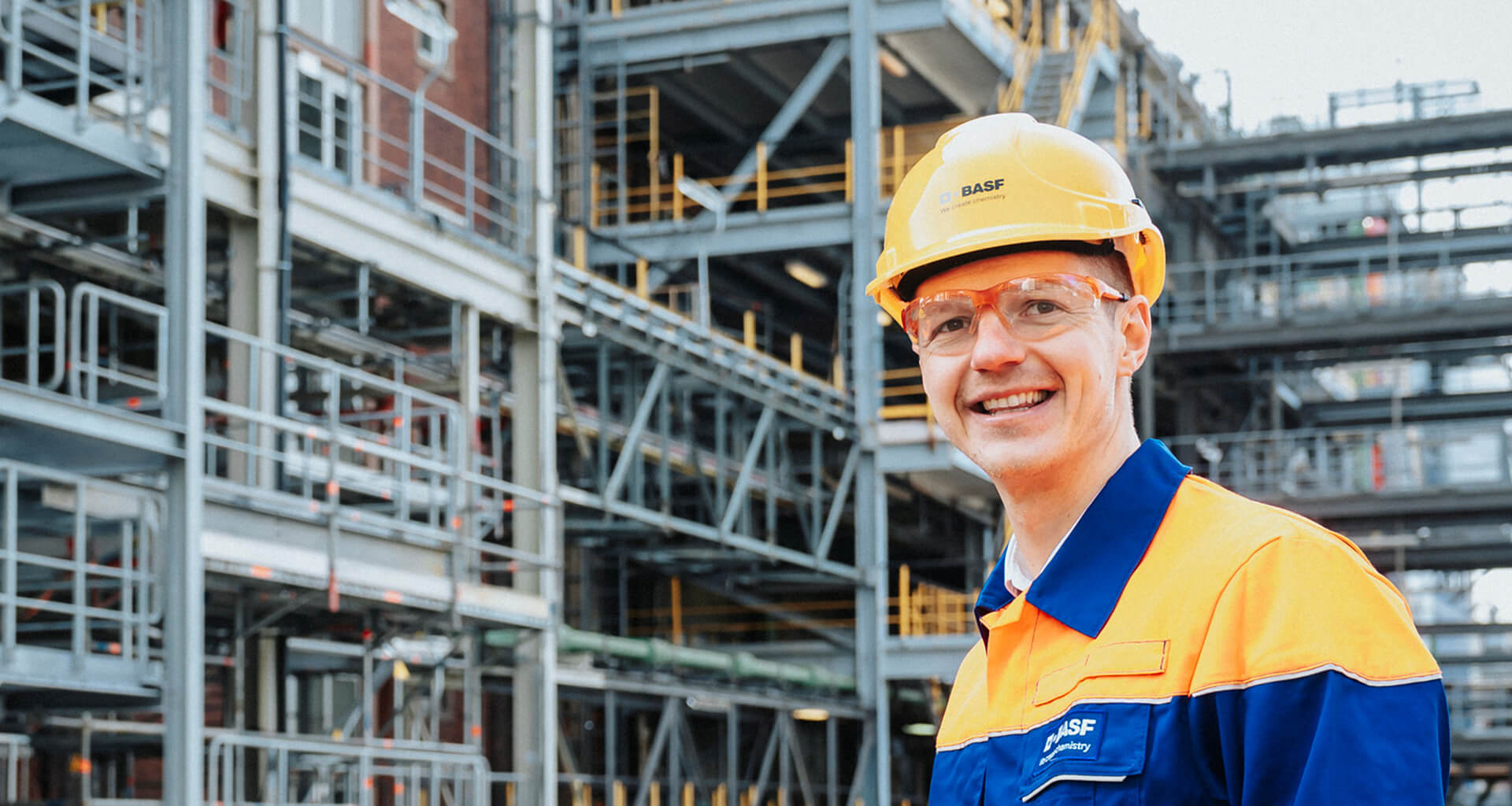
„Wir werden künftig einen Mix aus verschiedenen Verfahren und Technologien benötigen, um die ambitionierten Klimaschutzziele erreichen zu können.“ Neben der Methanpyrolyse beschäftigt sich BASF daher auch intensiv mit der Wasserelektrolyse zur CO2-freien Herstellung von Wasserstoff. Gemeinsam mit Siemens Energy werden derzeit am Standort Ludwigshafen erste Konzeptionsplanungen für den Bau eines PEM-Wasserelektrolyseurs (Proton Exchange Membrane) mit einer Leistung von 50 Megawatt erarbeitet und Möglichkeiten zur Projektförderung ausgelotet.
Neue Wege auch beim Steamcracker
Ein weiteres Beispiel für den klimafreundlichen Umbau der Produktion sind alternative Heizkonzepte für Steamcracker-Öfen. In diesen riesigen Anlagen wird Rohbenzin mithilfe von Dampf (steam) bei rund 850 Grad Celsius in Olefine und Aromaten aufgespalten (crack) – beides wichtige Grundbausteine für viele Wertschöpfungsketten in der Chemie. Bislang werden die benötigten Temperaturen durch die Verbrennung von Gas erreicht, was hohe CO2-Emissionen verursacht. Mit dem „eFurnace“ will BASF hier neue Wege gehen. „Unser Ansatz beinhaltet ein grundlegend neues Beheizungskonzept mit elektrischer Widerstandsheizung. Dies würde uns den Einsatz regenerativer Energien ermöglichen, wodurch wir künftig bis zu 90 % der prozessbezogenen CO2-Emissionen vermeiden könnten“, erklärt Dr. Andrea Haunert, Projektleiterin im BASF-Unternehmensbereich Petrochemicals. Um die Technologie weiterzuentwickeln und zu pilotieren, hat BASF im Jahr 2021 eine Kooperationsvereinbarung mit den Unternehmen SABIC und Linde unterzeichnet. Gemeinsam haben die Partner Fördermittel für den Bau einer Demonstrationsanlage beantragt.
-90%
mögliche Emissionsreduktion durch Umstieg auf eFurnace
Strombedarf wird deutlich steigen
Bis die verschiedenen innovativen Verfahren für eine klimafreundliche Produktion Realität werden können, sind in den kommenden Jahren noch viele verfahrenstechnische Herausforderungen zu meistern. Und ein weiterer Punkt ist entscheidend: Bei fast allen innovativen Technologien des Carbon-Management-Programms resultiert die CO2-Vermeidung daraus, dass die benötigte Energie nicht mehr aus fossilen, sondern aus erneuerbaren Quellen stammt – insbesondere aus Grünstrom. Durch die Umstellung auf die neuen, CO2-armen Produktionsverfahren würde BASF nach ersten Schätzungen allein am größten Standort Ludwigshafen künftig rund drei bis vier Mal so viel Strom benötigen wie heute. Für die Elektrifizierung der Steamcracker-Öfen bräuchte es beispielsweise die Leistung von ungefähr 100 Offshore-Windrädern. „Es ist also notwendig, dass möglichst viel erneuerbarer Strom produziert wird und zu den industriellen Großverbrauchern gebracht werden kann“, so Dr. Roland Merger, bei BASF verantwortlich für Projekte zur Versorgung der Chemieproduktion mit erneuerbarem Strom. „Wenn die Energietransformation gelingen soll, müssen deutlich mehr Flächen für die Produktion von erneuerbarem Strom freigegeben und die Stromnetze schnell in erheblichem Maße ausgebaut werden, damit ein ausreichendes Angebot an erneuerbarem Strom auf dem Markt vorhanden ist“.
Net Zero Accelerator
Anfang 2022 hat die neue Einheit „Net Zero Accelerator“ ihre Arbeit aufgenommen. Dort werden alle Kräfte gebündelt, die notwendig sind, um die CO2-Emissionen von BASF bis 2030 um 25 % zu reduzieren und bis 2050 auf Netto-Null abzusenken. Im Fokus stehen dabei drei Schwerpunkte: Erstes wichtiges Thema sind CO2-arme und CO2-freie Technologien – so genannte „Low Carbon Emission Technologies“. Dazu gehört etwa die Methanpyrolyse. Zweiter Themenkreis ist die Versorgung der BASF-Standorte mit erneuerbaren Energien, zum Beispiel durch Offshore-Windparks. Drittens geht es um Projekte zur Kreislaufwirtschaft, etwa das ChemCyclingTM-Projekt oder erneuerbare Rohstoffe.